GoKart - Mechanical
This project is mainly a collection of different mechanical aspects of the gokart worked on over time. Because the gokart has been assembled over the course of many years, a lot of the documentation does not exist or has been lost.
History
The project originally started around the winter of 2015. The original gokart (known as version 1) was functional but flawed in its design, mainly due to the weak frame and poor construction. The second gokart was built in late 2016, which featured improvements on almost every aspect. The frame was entirely redesigned, as well as the transmission—switching from a single centrifugal clutch to a torque converter with belt and chain.
Between 2018-2020 the gokart saw stagnation in its improvement, and any modifications made were purely to fix broken components. As of the summer of 2020, a complete rebuild of the vehicle was begun. While the majority of the components were recycled, some much needed upgrades were to be made.
Improving the Frame
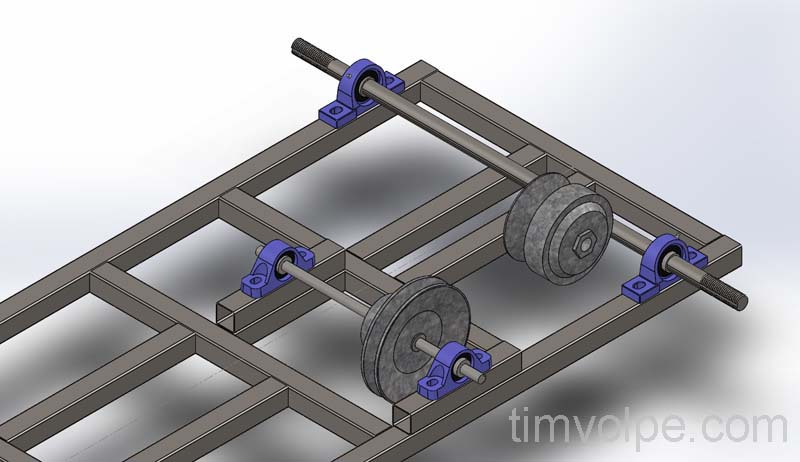
An issue with version 2 of the gokart was that the holes were very poorly drilled, resulting in lack of parallelism between drivetrain components, difficulty reinstalling components, and drifting of components during operation. This caused a major issue when the chain would come loose due to the jackshaft and back axle moving apart. A quick fix was to weld a plate holding the pillow block in place, but this was a pretty nasty hack.
To rectify this, all the holes would be re-drilled with much better precision. The first step was filling in the original holes. The MIG welder was used to slowly patch each hole with metal. The patches were then ground flush, and checked for penetration visually. Then a drill press was used to drill the new holes, with the help of a laser level, caliper and speed square for precision. The resulting holes were much more true to the design, and prevented the components from drifting during operation. Additionally, the entire drivetrain was better aligned with the frame to reduce wear on the bearings.
Another improvement made to the frame was simply fixing welds with poor penetration. The frame was originally stick welded, which was extremely difficult due to the thin metal tube. Because of this, there were some spots where blow-outs were never properly fixed. With the gentler heat of the MIG welder, these spots could finally be fixed to increase the frames strength.
Improving the Steering
The steering was far from perfect due to the difficulty of accurately designing and building a robust steering system. One major issue with a simple fix, however, was the weak attachment of the steering column. Because of the geometry, the steering column was at an unfavorable angle in relation to the frame with no support. Every time the vehicle hit a bump, the operator would inadvertently push up or down on the column which put a large amount of torque on the weld. To rectify this, gussets were added to prevent the column from flexing as much under load and increase weld area.
The steering column sheath, which the actual steering shaft rotates in, was also not correctly affixed to the vehicle. It was only held on with pipe clamps, because it was much easier than welding. This was replaced by actually welding the sheath to the vehicle. This task was somewhat difficult, as uneven heating would cause warpage that would bind up the shaft.